پایش خوردگی
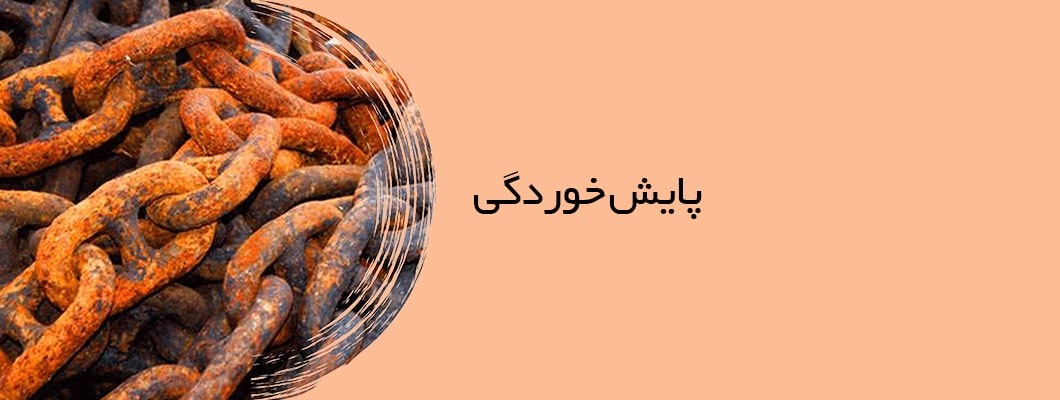
تخریب شدن یک ماده در اثر واکنش با محیط پیرامون آن را خوردگی میگویند و این تعریف هم فلزات و هم غیرفلزات را در بر میگیرد. سرعت تخریب با توجه به نوع ماده و محیطی که در آن قرار میگیرد، میتواند سریع یا کند باشد. در تعریفی دیگر، خوردگی فلزات را میتوان بر عکس فرآیند متالورژی استخراجی بیان کرد. در طی فرآیند متالورژی استخراجی، فلز از سنگ معدن که خود حاوی اکسیدهای فلز است استخراج میشود ولی در خوردگی، فلز در اثر واکنش با محیط اکسید شده و در اصطلاح خورده میشود. خوردگی آهن و آلیاژهای آن به اصطلاح زنگ زدن نامیده میشود، اگرچه دیگر فلزات نیز هنگام خوردگی به اکسید تبدیل میشوند ولی دیگر از واژه زنگ زدگی استفاده نمیشود. در هر صنعتی که درگیر فرآیندهای نفت و گاز و مواد فرار است، خوردگی می تواند یکی از بزرگترین تهدید های طول عمر و پایداری دارایی باشد. پایش خوردگی یا مونیتورینگ خوردگی، استفاده از تجهیزات اندازه گیری میزان خوردگی به عنوان پایش پیوسته خوردگی یا خورندگی روی یک تجهیز با ارزش در نظر گرفته و تعریف شود. روشهای بسیاری برای مقایسه میزان نرخ خوردگی واقعی و پیش بینی شده و یا اندازه گیری برای جلوگیری از خوردگی و یا تعدیل آن انجام می شود. اما همه پایش های خوردگی به میزان فرسایش که در پروسه پلنت و با دبی بالا یا ذرات جامد اتفاق می افتد حساس نیستند. تجهیز با ارزش مورد نظر می تواند لوله، پل های بتنی، سیستمهای تهویه مطبوع در ساختمانهای بزرگ، یا امکانات مجموعه های نفت و گاز باشد. بدون مانیتورینگ و پایش مناسب، مخازن صنعتی بزرگ مثل مخازن فشار و بویلرها به تدریج دچار خوردگی شده و تخریب و نشتی رخ میدهد که منجر به کاهش بازدهی و قابلیت اطمینان می شود. در موارد شدید، اگر خوردگی مورد پایش قرار نگیرد، منجر به تخریب کامل دارایی و انفجار و تهدید جان پرسنل و به بار آمدن خسارات سنگین مالی و محیط زیستی می شود. پایش خوردگی به معنی مشاهده و چک کردن تغییرات متریال (فلزات، بتن و…) به واسطه فرآیندهای تخریب مانند زنگ زدگی اتمسفری، محلول شیمیایی، کریستالیزاسیون، واکنش زوج های گالوانیکی و… در تجهیزات با پروب های خوردگی یا دیگر ابزارهای مناسب است، به عبارت ساده تر پایش خوردگی دنبال کردن تخریب تجهیزات در طول زمان است. پل ها و سایر سازه های بتنی خراب می شوند و حتی اگر اقدام به نظارت و جلوگیری از خوردگی میلگرد انجام نشود، ممکن است سقوط کنند. خوردگی میلگرد اغلب آشکار نشده است و روش های پیشگیری از خوردگی تحت استفاده هستند. خوردگی مسئله ای است که همه صنایع مختلف به نوعی در زندگی روزمره با آن درگیر هستند و اگر هزینه هایی را برای حفاظت از آن متقبل نگردند مجبور به پرداخت هزینه های سنگین ناشی از عدم کنترل و پایش خوردگی خواهند بود.
علل خوردگی
استفاده از نفت خام سنگین و فوق سنگین به عنوان خوراک، آب دریا به عنوان سیال گردشی خنک کننده ماشین آلات، سیالات حاوی نفت و گاز ترش و خورنده و ...سبب افزایش خوردگی تجهیزات پالایشگاه و خطوطه در صنعت نفت و گاز و نیز سیالات با شرایط خورندگی در صنایع دیگر می شود.
انواع خوردگی
دسته بندی های مختلفی برای انواع خوردگی وجود دارد، در یک دسته بندی، خوردگی به دو نوع خشک و تر تقسیم می شود: منظور از خوردگی تر، خوردگی در حضور آب و یا یک مایع خوردنده میباشد. خوردگی خشک در حضور اتمسفر گازی و یا در تماس با جامدات صورت میگیرد. دستهبندی دیگری که برای انواع خوردگی بیان میشود بر اساس نحوه شناسایی و تشخیص میباشد: خوردگیهایی که با بازرسی چشمی مشخص میگردند مثل: خوردگی یکنواخت، خوردگی موضعی و خوردگی گالوانیک. خوردگیهایی که برای تشخیص نیاز به چشم مسلح دارند مثل: خوردگی سایشی و خوردگی بین دانهای. خوردگیهایی که نیاز به میکروسکوپ برای تشخیص دارند مثل: خوردگی خستگی، خوردگی دما بالا و خوردگیهای میکروبی. یکی از بهترین تقسیم بندیهای خوردگی توسط انجمن مهندسان مکانیک امریکا صورت گرفته است که انواع خوردگی را در شش دسته بیان کرده است.
محافظت از خوردگی
استفاده از روشهای حفاظت کاتدی به دو صورت آند فداشونده یا جریان اعمالی، تزریق مواد شیمیایی و بازدارنده های خوردگی، اعمال پوشش های متناسب برای سطح های مختلف فلزی حفاظت از خوردگی را از جمله روش های جلوگیری از خوردگی برشمرد.
تفاوت پایش خوردگی و بازرسی خوردگی غالبا در استفاده از واژه های “ پایش و نظارت“ و ”بازرسی“ خوردگی، کمی گیج شدن وجود دارد وقتی که برای اندازه گیری میزان از بین رفتن فلز و محاسبه میزان خوردگی در مصارف صنعتی مانند نفت و گاز ، تصفیه آب، پلنتهای شیمیایی استفاده می شود. تفاوت مشخصی بین این دو وجود دارد. بازرسی به معنی بررسی مکرر نقاط، برای بررسی تغییرات یا انحراف از نتایج پیش بینی شده یا مورد نیاز است. در حالی که نظارت و پایش به عنوان بررسی مداوم به منظور کنترل با هدف واکنش سریع در برابر تغییر تعریف می شود. در هنگام استفاده از روشهای محاسبه نرخ خوردگی در لوله ها و مخازن، درک تفاوت بین این دو و انتخاب فن آوری مناسب برای دستیابی به اهداف مورد نظر مهم است.
به عنوان مثال اگر هدف، ارزیابی یا تخمین زمانی است که دیواره یک لوله یا مخزن خورده شده و به حد بیشترین میزان مجاز خوردگی خود رسیده که باید تعویض شود، ممکن است تکنیک های بازرسی مناسب باشند. اما اگر هدف مانیتورینگ مداوم فرآیند خوردگی و نظارت بر آن بوده و اقدامات الزم جهت کاهش میزان خوردگی انجام شود، تا عمر تجهیزات، افزایش و هزینه ها کاهش یابد ، این امر تنها با مونیتورینگ مداوم خوردگی با حساسیت بالا حاصل می شود.
جلوگیری و کنترل خوردگی
به طور کلی روشهای مقابله با خوردگی به چند دسته زیر تقسیم میشوند. بیان جزئیات به پستهای آتی واگذار میگردد.
1- انتخاب مواد مهندسی مناسب: مهندسان مواد (با تخصص شناسایی و انتخاب مواد مهندسی) براساس خواص فیزیکی، مکانیکی، حرارتی، شیمیایی و غیره مورد نیاز سرویس میتوانند موادی را پیشنهاد دهند که معضلات ناشی از عدم سازگاری با شرایط محیط و سرویس و در نتیجه تخریب را به حداقل برسانند.
2- استفاده از رنگ و پوششهای محافظ: مهندسان مواد و پلیمر متخصص در زمینه رنگ و پوشش و همچنین اظهار نظرات بازرسهای رنگ میتواند به ارائه و اجرای انواع رنگها و پوششهای ضدخوردگی در سطوح حساس شود. این روش منجر به جلوگیری از بسیاری از خوردگیهای اتمسفری و خصوصا اتمسفر دریایی میشود و باعث افزایش عمر بسیاری از سازههای ساحلی و کشتیها میشود.
3- حفاظتهای کاتدی و آندی: مهندسان مواد (با تخصص خوردگی و حفاظت از فلزات) میتوانند در بسیار موارد و خصوصاً سازههای مدفون در خاک که در معرض خوردگی گالوانیک شدید محیط خورنده خاک، سیستمهای حفاظت از خوردگی را طراحی و اجرا کنند.
4- استفاده از ممانعت کنندهها: محلول ضدزنگ مورد استفاده در ماشین مثال خوبی از ممانعت کنندههای خوردگی است. مطالعات مهندسان شیمی و مواد منجر به تولید محلولهای شیمیایی با ترکیبهای مختف شده است که میتواند با تشکیل یک لایه مولکولی محافظ از واکنشهای الکتروشیمیایی و خوردگی جلوگیری کنند.
مزایای روشهای پایش خوردگی
- گزارش احتمال ازکارفتادگی سیستم در یک مدت زمان مشخص که ناشی از وجود خوردگی است.
- مطالعهی تغییرات و اصلاحات موجود در پارامترهای سیستم و تاثیر آنها بر خورندگی محیط.
- شناسایی خوردگی در سیستم، دلایل ایجاد و اثرات آن و پارامترهای کنترل نرخ خوردگی مانند فشار، دما، pH و سرعت جریان.
- ارزیابی اثر تکنیکهای کنترل و جلوگیری از خوردگی مانند ممانعتکنندههای شیمیایی و محاسبهی روشهای بهینه.
- مدیریت اطلاعات مربوط به امکانات موردنیاز برای نگهداری سیستمهای در حال کار.
نظر خود را بنویسید