میکرواهم متر و سیم و کابل
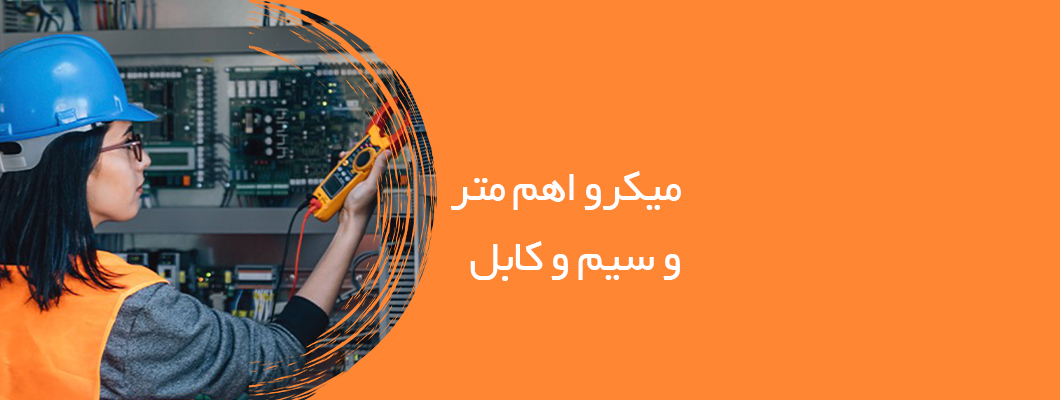
میکرواهم متر و سیم و کابل
در فرایند تولید سیم و کابل، مهمترین بخش کنترل کیفیت و آزمایشگاه میباشد که بایستی در هر کارخانه وجود داشته باشد. در این مرحله مقاومت الکتریکی سیم هادی و روکش، مقاومت در مقابل کشش، سرما و … آزمایش شده و پس از تائید روانه بازار میگردد. واحد كنترل و كيفيت به منظور صرفه جويي در هزينه هاي دوباره كاري و جلوگيري از بروز ضايعات و جهت نيل به اهداف خط مشي کيفيت سازمان/ شرکت و همچنين حصول اطمينان از رضايت مشتري براساس استاندارد 9001 ISO بوجود آمده است.
پيش از شروع توليد بايد تصميم گرفته شود که چه چيزي با چه مشخصاتي قرار است توليد شود. پس از آن توليد شروع مي شود و در نهایت بايد بررسي شود که آيا محصول توليد شده با مشخصات تدوين شده از جمله استانداردها مطابقت دارد يا خير؟ کيفيت محصول به هر سه عامل طرح، توليد و بازرسي مربوط است و کنترل کيفيت آماري ابزاري است که در تصميمات مربوط به هر سه عامل فوق به کار گرفته مي شود و با استفاده مؤثر از تکنيک هاي آماري مي توان بين مسئولين بخشهاي طراحي، توليد و بازرسي هماهنگي ايجاد نمود.
در صنعت سیم وکابل به دلیل اینکه استانداردهای مدون و اجباری چارچوب لازم الاجرا برای تعیین استانداردها جهت مشخصات کیفی انواع کابل هاست، بکارگیری بروشورهای استاندارد ملی و علاوه بر آن بکارگیری استانداردهای بین المللی نظیر ASTM و نیز استانداردهای کارخانه ای به منظور حفظ کیفیت محصول و تدوام آن در طول عمر مفید کابل امری ضروری است.
واحد کنترل کیفیت سیم وکابل، مسئولیت تضمین کیفیت محصولات تولیدی را از لحاظ کیفی و کمی بر عهده دارد؛ لذا طبق سیستم مدیریت کیفیت ؛
فرایندهای کنترل در سه گروه به شرح زیر می باشد:
1. کنترل اقلام ورودی
تمامی مواد اولیه موثر بر کیفیت محصولات نهایی تحت کنترل می باشند، یعنی مشخصات فنی برای هر کدام از مواد اولیه طبق استانداردهای مربوطه تعیین و در برگ مشخصات فنی (MS) به همراه محدوده های کنترل و معیار پذیرش تعریف شده است. واحد بازرگانی خرید مواد اولیه را از لیست تامین کنندگان مجاز بر اساس همان روش اجرایی انجام و پس از بازرسی و انجام آزمایشات لازم در آزمایشگاه به تایید واحد کنترل کیفیت می رساند. مواد اولیه تایید شده در انبار می تواند به عنوان مواد اولیه مصرفی در واحد تولید باشد.
2.بازرسی حین فرایند
طبق روش اجرایی کنترل کیفیت برای هر کدام از دستگاه ها که یک فرایند از تولید تعریف میشود ایستگاه های کنترل در بخش تولید تعیین شده است و پارامتر های کنترل نیز به همراه تعداد نمونه برداری و معیارهای پذیرش تعیین و در فرم های روزانه کنترل کیفیت ثبت می شود. در صورت مطابقت مقادیر ارزیابی هر قرقره از محصولات و با تایید آن توسط بازرس خط، اجازه استفاده در فرایند بعدی صادر می شود. نتایج ثبت شده روزانه واحد کنترل کیفیت، در بهبود مستمر سیستم مدیریت کیفیت و در تجزیه و تحلیلهای آماری به صورت ماهانه، سالانه برای ایجاد فرصت های بهبود مورد استفاده قرار می گیرد.
در صورت وجود عدم انطباق در حین فرآیند تولید، دستور توقف تولید از سوی واحد کنترل کیفیت به واحد تولید صادر گردیده و اقدامات اصلاحی در جهت رفع موارد انجام می پذیرد.
3.بازرسی محصول نهایی
از هر یک از محصولات نهایی خروجی از تولید شامل هادی های هوایی بدون روکش، روکش دار، کابل قدرت و خودنگهدار به صورت تصادفی یک نمونه تهیه و جهت انجام آزمون های نمونه ای به آزمایشگاه کنترل کیفیت ارسال می گردد.
در قسمت بازرسی نهایی دو آزمون اندازهگیری مقاومت الکتریکی هادی و آزمون های ولتاژ روی صددرصد محصولات تولیدی انجام می گیرد. در صورت وجود عدم انطباق در محصول نهایی، قرقره توسط واحد کنترل کیفیت به انبار قرنطینه انتقال یافته و موارد جهت تصمیم گیری و اقدامات اصلاحی طی فرم کنترل محصول نامنطبق به هماهنگی واحد کنترل کیفیت، تولید و مدیریت عامل انجام می شود.
انواع آزمون هایی که در آزمایشگاه انجام می گیرد به شرح زیر و همراه چند آزمایش آورده شده است:
آزمون های الکتریکی
دستگاه آزمون های ولتاژ: : انجام آزمون ولتاژ بالا و تست نشتی بر روی عایق کابل
دستگاه آزمون مقاومت عایقی (میگر): اندازه گیری مقاومت الکتریکی عایق ها
دستگاه میکرو اهم متر: اندازه گیری مقاومت ویژه و الکتریکی هادی ها
آزمون های ابعادی و دمایی و کمی
کولیس، میکرومتر، ساعت اندازه گیری دیجیتال، خط کش و متر: جهت اندازه گیری دقیق ابعادی سیم و کابل و روکش و …
دماسنج، رطویت سنج دیجیتال: جهت اندازه گیری و کنترل دما
پروفایل پروژکتور و مقطع نما دیجیتال: جهت اندازه گیری ضخامت عایق و روکش با دقت بالا
ترازوی دیجیتال: جهت اندازه گیری اوزان
تجهیزات مکانیکی
دستگاه چند منظوره کشش: انجام ازمون مکانیکی (استحکام کشش و ازدیاد طول مواد فلزی و پلاستیک، آزمون های پیر سازی و کهنگی)
دستگاه پیچش: جهت آزمون های پیچش و خمش و چسبندگی روکش مفتول های فولادی
آزمون های دمای بالا و پایین
فریزر جهت آزمون خمش و پیچش در دمای پایین، آزمون ضربه در سرما
آون جهت آزمون فشار و حرارت، شوک حرارتی، آزمون گرماسختی، آزمون جمع شوندگی
آزمون های شیمیایی
جهت انجام آزمون تعیین مقدار روی
یکنواختی روکش بر روی فولاد گالوانیزه
آزمونهای محیطی
از آنجایی که یکی از کاربرد های اصلی سیم و کابل ها، استفاده در تجهیزات و دستگاه هایی است که در معرض آسیب های محیطی نظیر آب، خوردگی و … می باشند، آزمون های محیطی با هدف برسی این ویژگی از محصولات و رفع عیوب احتمالی آنها، طراحی و در دست اجرا قرار گرفته اند. این آزمون ها شامل آزمون های مقاومت در برابر آب، مقاومت در برابر خوردگی و مقاومت در برابر اشعه ماورا بنفش می باشند.
در ازمون برسی مقاومت در برابر آب، کابل در برابر آب قرار داده می شود و سپس از نظر میزان نشتی و آسیب ، مورد ارزیابی قرار خواهد گرفت.
در ازمون های برسی مقاومت در برابر خوردگی، برای مدتی معین، محصول در معرض محیط خوردنده به منظور تعیین میزان خورندگی، قرار خواهد گرفت.
با قرار دادن کابل در برابر اشعه ماورا بنفش و تعیین میزان تغییر رنگ و آسیب به وجود آمده نیز، مقاومت در برابر اشعه ماورا بنفش سنجیده خواهد شد.
آزمون های حرارتی
دسته ای دیگر از آزمون های انجام شده در ازمایشگاه به منظور کنترل کیفیت کابل ها و سیم های تولیدی، آزمون های حرارتی می باشند که در طی آنها، محصول نهایی به منظور تعیین تحمل گرمایی به مدت ۶۰ ثانیه در برابر شعله مستقیم قرار خواهد گرفت و در جهت تعیین میزان خمش و پیچش در سرما، به مدت مشخصی دردرون فریز های مخصوص قرار می گیرد.
نظر خود را بنویسید