روش تولید سیم و کابل
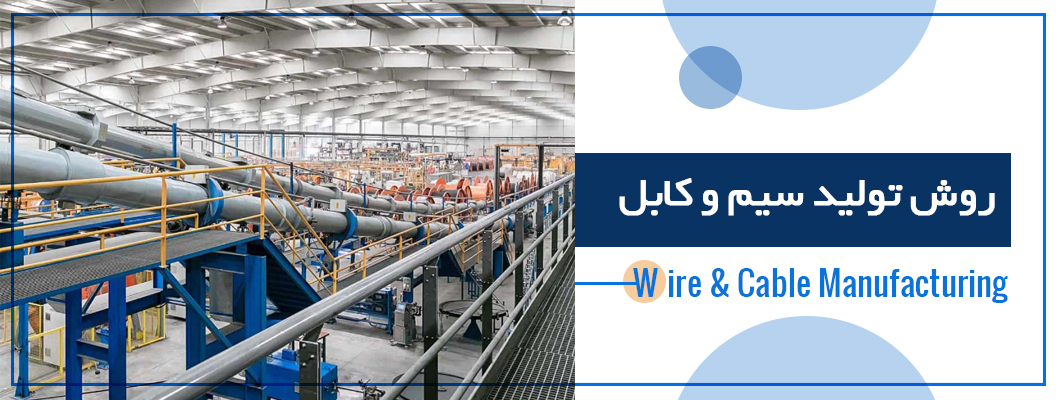
Manufacturing process
- wire drawing:در مرحله ی اول هدف آماده کردن سیم مسی یا آلومینومی طبق استاندارد AWGاست. روش به دست آوردن میله مسی یا آلومینومی به وسیله ی قالب های الماس مصنوعی است که به تدریج اندازه ی آنها کاهش می یابد. در این روش از یک سیم روان کننده برای افزایش عمر قالب استفاده می کنیم و از گرم شدن سیم جلوگیری می کنیم.
- Annealing: در این مرحله فشار زیادی را به سیم اعمال می کنیم بنابراین سیمی که به دست می آوریم بسیار شکننده است و در صورت خم شدن به راحتی شکسته می شودباید حتما به این نکته توجه داشت این سیم ها باید انعطاف پذیر باشد.
- Twisting and stranding: در این مرحله دو یا چند سیم هم زمان با استفاده از فرمول اختصاصی برای تعیین طول سیم به هم پیچ خواهد خورد.
- Extrusion:سیم انعطاف پذیر از طریق الکترود عبور داده می شود مواد مورد نظر در بخش انتهایی الکترود ریخته می شود سپس در حین گرم شدن به قسمت جلویی الکترود رانده می شود.سیم روکش شده با خارج شدن از الکترود وارد سیستم خنک کننده می شود و روی حلقه ها پیچیده می شود.
- Cabling:کارهای اصلی ساخت کابل به پایان می رسد،از این مرحله به بعد سر هم کردن کابل ها مد نظر است این فرآیند در ایستگاه کابل کشی انجام می شود.برای کابل های الکتریکی و الکترونیکی که در روز استفاده می کنیم به بسته شدن یک یا چند سیم استرند شده برای حفاظت کابل در برابر تداخل نیاز داریم. هم چنین برای این که شکل بهتری داشته باشد از filler استفاده می کنیم تا شکل نهایی کابل گرد باشد.
تجهیزات تولید سیم و کابل
- دستگاه کشش اولیه مفتول: این مرحله با نازک کاری مفتول های مس به قطر 8 میلی متر و یا مفتول های آلومینیوم به قطر 5/9 میلی متر شروع می شود و در صورت نیاز با خروجی های به قطر 38/1 تا 55/3 میلی متر می توان از دستگاه های دیگر کشش نیز استفاده نمود و قطر مفتول را تا حد 1/0 میلی متر کاهش داد .
انواع کشش با توجه به سایز ورودی و خروجی مفتول به طور کلی به سه دسته راد ، مدیوم و فاین تقسیم می شود . فرآیند آنیل کاری برای ایجاد نرمی در مفتول کشیده شده می تواند به صورت همزمان یا پس از عملیات کشش در کوره صورت پذیرد .
- دستگاه کشش متوسط
- دستگاه کشش فاین آنیل پیوسته
- دستگاه کشش فاین نهایی
- دستگاه تک سیمه 5 دستگاه اکسترود روکش سیم
- دستگاه اکسترودر غلاف
- بانچر (تاباننده سیم) با متعلقات تا 22 رشته داخلی:برای تابیدن رشته های افشان و نیمه افشان ( در مقطع کم ) به کار می رود.
- استرندر 1 دستگاه 7 رشته:برای تابیدن رشته های لخت هادی در هادی های نیمه افشان مقطع بالا و همچنین تابیدن رشته های عایق دار مقطع پایین استفاده می شود.
- استرندر 19 رشته برای کابلهای کنترل
- دستگاه کویلینگ دستگاه کلاف ساز
- دستگاه بستهبندی کابل:برای تابیدن رشته های عایق دار مقطع بالا از آن استفاده می شود.
- دستگاه جوش گرم و نازک کن برای جوش مفتول
- دستگاه ریوایندینگ پیچ قرقرهها
- دستگاه جوش سرد برای جوش مفتول سیم
- تجهیزات تست و کنترل کیفیت
- سیستم مانیتورینگ و کنترل خط تولید
- پودر پاش
- جت پرینتر و مارکر
تولید سیم و کابل در ایران
- ابتدا مفتول 8 میلیمتر مس که روی قرقره های بزرگی قرار گرفته به وسیله ی لیفتراک روی سکو قرار میگیرد وارد دستگاه کشش می شود و در قرقره ی غالب قرار می گیرد،به قطرهای بزرگتر پیچیده می شود. از آن جایی که حین تولید سیم یا کابل نور و حرارت زیادی تولید می شود معمولا دستگاه کشش را روغن کاری می کنند.
- سیم ها به دستگاه کشش ثانویه فرستاده شده و به قطرهای متفاوتی تقسیم می شوند سپس سیم ها درون مخزن فلزی کوره چیده شده و توسط جرثقیل به کوره ی آنیل هدایت می شوند.عملیات حرارت دادن به سیم باعث می شود که سیم حالت خشکی خود را از دست بدهد و نرم و منعطف شده و در نتیجه در بانچر آسیب نبیند.
- بعد از مرحله آنیلینگ سیم وارد بانچر شده و دور قرقره پیچیده می شود سپس یک عایق پلاستیکی دور سیم ها توسط دستگاه اکسترودر کشیده می شود.
- سیم ها بعد از روکش دار شدن وارد دستگاه چاپ می شوند و مشخصات سیم و کارخانه روی آن ها ثبت می شود.
- سیم ها پس ار تولید وارد دستگاه کلاف کن می شوند که سیم ها را دسته بندی می کند.
- مهم ترین مرحله ی ساخت سیم و کابل کنترل کیفیت سیم می باشد که مقاومت سیم،هادی،عایق رصد می شود .
توجه:هرگونه کپی برداری از مقاله با ذکر منبع و ارائه ی لینک مقاله بلامانع است.
نظر خود را بنویسید